
I learned at an early age that delivering customer value, meeting clear customer expectations, and operating with professionalism and integrity consistently is how you build trust and respect.

It was the relationships that helped my family’s business grow and most importantly survive during slower economic times. I witnessed firsthand on how my parents built strong and meaningful customer relationships by delivering genuine, positive customer experiences.
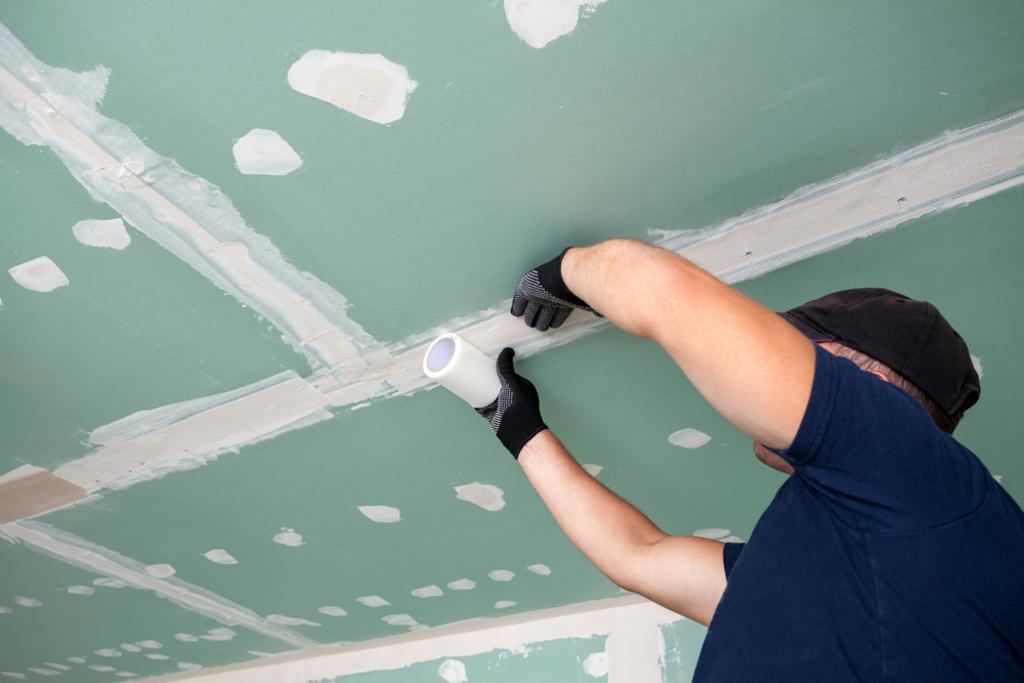
CertaPro Painting franchises are the largest residential painting company in the United States.īorn and raised in Midwest, I was involved in the trades early in life assisting in my father’s interior finishing business. After deciding to look for ways to improve, what follows is up to you to decide what makes the most sense for your operation.Donovan True is the president of CertaPro Painting of Renton/Kent, WA. The goal of increasing throughput and reducing cycle times will dictate change… a change in mindset, workflow, process, and maybe even the products and tools primarily used in your facility.
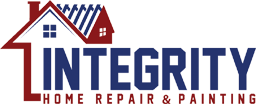
Mark Thomas, National Training Manager, U-POLĬycle time is one of the many metrics collision repair shops use to gauge their operational efficiency.Dan Reutter, Technical Specialist, U-POL.Time and energy savings advantages of combining key U-POL products in the filling and priming stages of repair.Ways to increase throughput and reduce cycle time.Potential bottlenecks that can slow down the repair process.In this 60-minute session, we will explore: Whatever can be done to shorten the time it takes to repair and return a vehicle is critical to achieving high customer satisfaction rates and maximizing throughput, so your business operates as smoothly as possible. Even though the measurement of cycle time does not officially begin until the necessary parts and repair materials are in technicians’ hands, this critical distinction in your process is irrelevant to the consumer. Cycle time is just one component in the measurement of key-to-key time, which most collision repair shops monitor to maintain a healthy business.
